How to Improve OEE
In manufacturing, every minute matters. Machines that don’t function well translate directly into lost revenue, wasted materials, and missed targets. That’s why OEE (Overall Equipment Effectiveness) is one of the most critical KPIs for operations leaders. It tells you how close you are to your plant’s full productive potential. OEE isn’t just a number but also a window into how your production lines perform and a guide to where you can unlock major gains. Let's break down the components of OEE, like the common causes of lost effectiveness, and most importantly, what manufacturers can do to improve it. Sustainably and at scale.
Customertimes
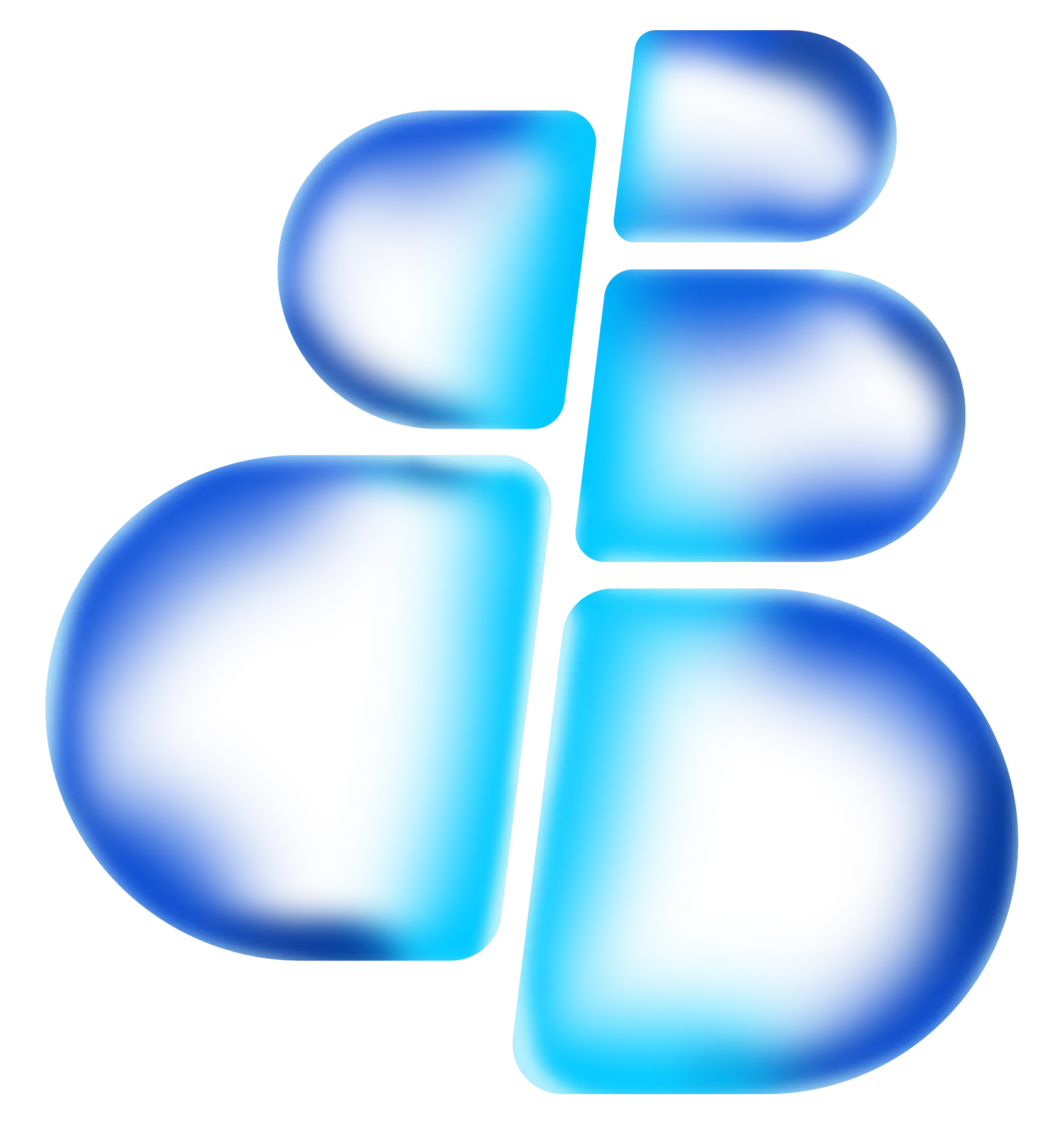
How to Improve OEE
In manufacturing, every minute matters. Machines that don’t function well translate directly into lost revenue, wasted materials, and missed targets. That’s why OEE (Overall Equipment Effectiveness) is one of the most critical KPIs for operations leaders. It tells you how close you are to your plant’s full productive potential. OEE isn’t just a number but also a window into how your production lines perform and a guide to where you can unlock major gains. Let's break down the components of OEE, like the common causes of lost effectiveness, and most importantly, what manufacturers can do to improve it. Sustainably and at scale.
Customertimes
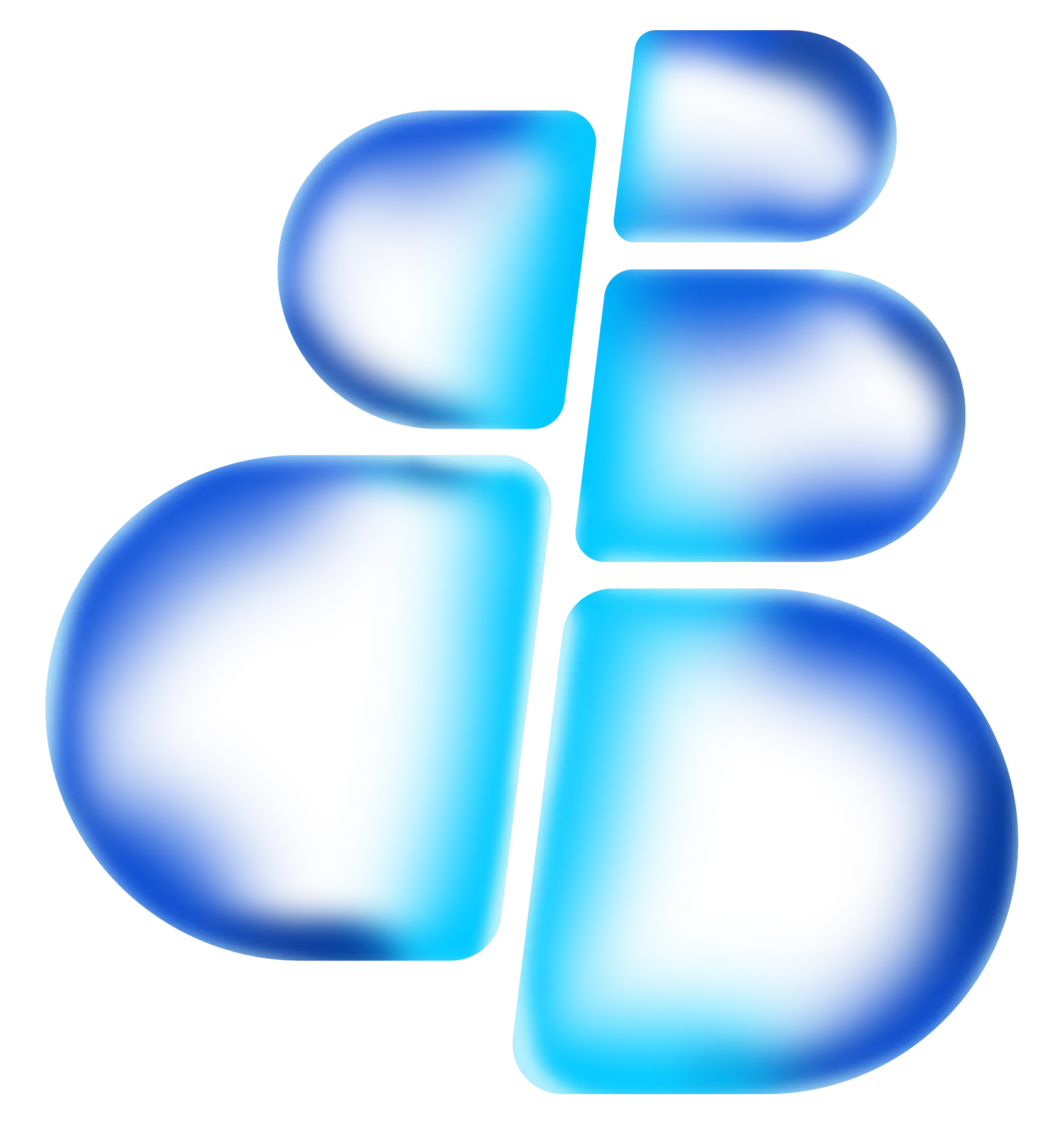
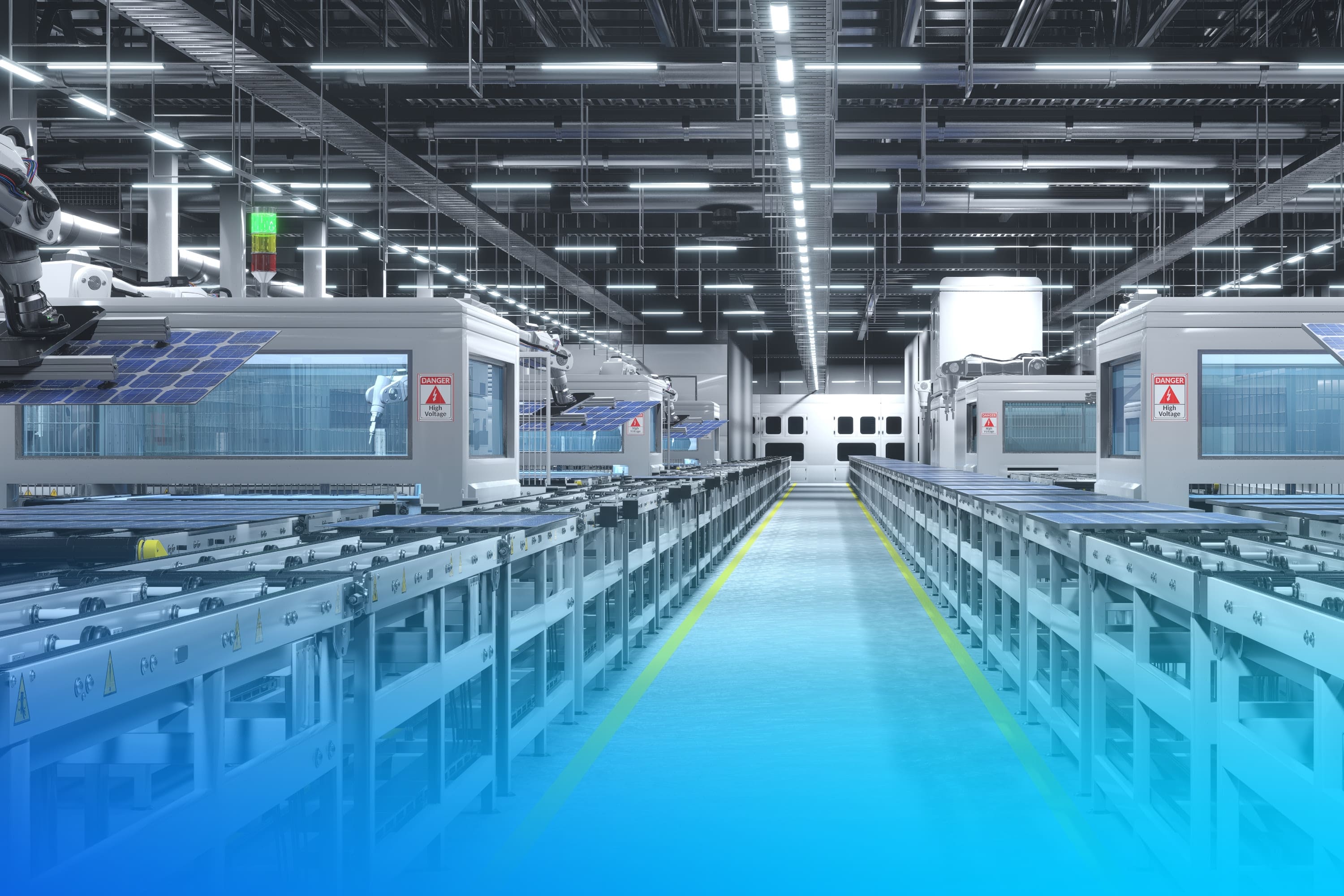
What Is OEE?
OEE combines three key metrics to deliver a single score that reflects how well your equipment is running:
- Availability – Are your machines running when they’re supposed to be?
- Performance – Are they running at optimal speed?
- Quality – Are they producing good parts?
Multiply those three percentages together, and you get your OEE score. A perfect score is 100%, but world-class manufacturers aim for 85% or higher.
Improving Availability - Cut Unplanned Downtime at the Source
If there’s one OEE pillar most manufacturers think they’re managing well, it’s availability. After all, if a machine isn’t running, it’s obvious, right? Not exactly.
The reality is that downtime is often underreported, misclassified, or normalized, especially in environments where operators are incentivized to "keep things moving" rather than document every interruption. As a result, the true cost of lost Availability (missed output, downstream disruptions, labor inefficiencies) is often underestimated.
Let’s look at the four most common causes of Availability loss, and what high-performing plants do differently.
Equipment Breakdowns
Unplanned mechanical or electrical failures are one of the most immediate and disruptive threats to equipment availability. A single faulty component can bring an entire production line to a standstill. When the root cause is not obvious or when spare parts are not readily available, downtime stretches longer and productivity losses increase.
These breakdowns are not only costly in terms of output, but they also cause scheduling disruptions, labor inefficiencies, and a ripple effect across downstream operations. Reacting after a failure occurs is no longer an effective strategy in modern manufacturing environments.
To prevent unplanned equipment failures and minimize their impact, manufacturers should take a more proactive and data-driven approach to maintenance. Practical steps include:
- Implementing predictive maintenance by using sensors to monitor vibration, temperature, pressure, or other key indicators. These tools can detect early signs of wear or instability that often precede failure, allowing teams to intervene before a breakdown occurs.
- Analyzing historical failure data to refine maintenance schedules and better understand which parts are most likely to fail. This information can be used to ensure that critical spares are in stock and that maintenance is timed more effectively.
- Equipping operators with digital tools that allow them to quickly report issues, log anomalies, or request maintenance support. Making it easy for frontline teams to flag small problems in real time helps prevent those issues from escalating into major breakdowns.
A successful maintenance strategy should not only prevent downtime but also support consistent equipment performance over time. By focusing on early detection, smart scheduling, and clear communication, manufacturers can reduce the risk of unexpected failures and improve the overall reliability of their operations.
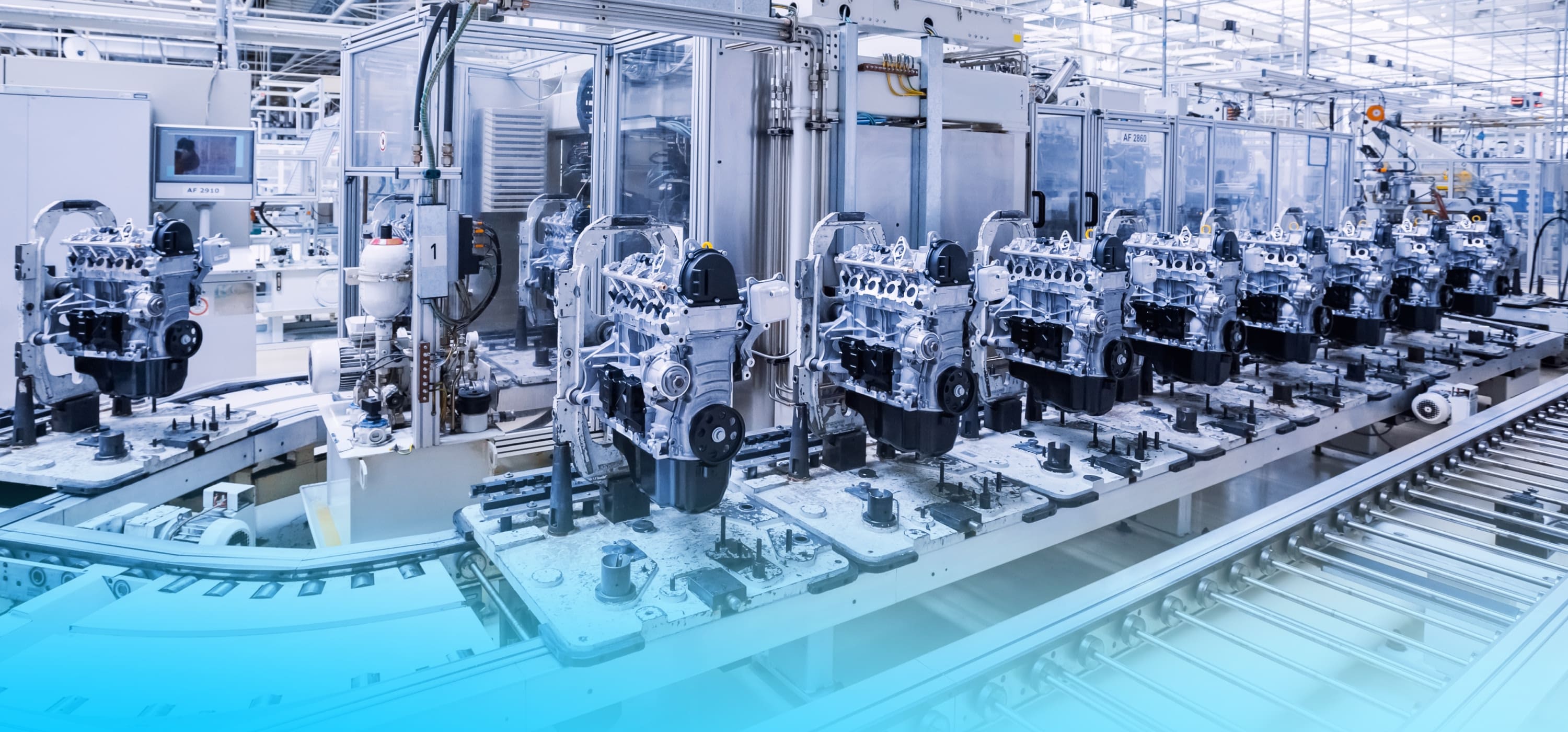
Changeovers and Setup Time
In high-mix manufacturing environments, frequent product changeovers are often a hidden but significant source of lost productivity. Each transition between product types introduces an opportunity for delay, especially when procedures are unclear or coordination between teams is lacking. These setup times can quietly consume valuable production hours and reduce overall equipment efficiency, even when the machines themselves are fully operational.
Because changeovers do not always result in a full line stoppage, they are easy to underestimate. However, the time lost during frequent setups adds up quickly, especially across multiple shifts or complex product lines.
To improve setup efficiency and reduce the impact of changeovers, manufacturers can take the following steps:
- Apply Single-Minute Exchange of Dies (SMED) techniques to streamline setup procedures. These methods are proven to reduce changeover times by 30 to 70 percent.
- Identify and separate internal and external tasks. Internal tasks are those that require the machine to be stopped, while external tasks can be completed while the equipment is still running. By shifting more tasks to the external category, teams can reduce total downtime during changeovers.
- Standardize best practices across all teams and shifts. Use digital checklists, visual instructions, or automated prompts to ensure that every operator follows the same steps, regardless of experience or time of day.
Improving changeover efficiency does more than increase equipment availability. It enhances overall plant agility, allowing for smaller batch sizes, faster response to customer orders, and more flexible scheduling without sacrificing output.
By treating changeovers as a process to optimize rather than a fixed cost of production, manufacturers can unlock significant performance gains with relatively small changes in routine.
Material Shortages and Logistics Delays
Even a brief interruption in material flow, such as five to ten minutes without the required inputs, can cause unplanned downtime and reduce overall efficiency. These pauses are often dismissed as minor planning issues, but they create recurring gaps that gradually undermine output, reliability, and the rhythm of production.
When machines are ready and operators are available, delays caused by missing components or late deliveries become especially frustrating. The equipment is in place, the labor is scheduled, but production stalls simply because the right materials are not where they need to be at the right time.
To improve material availability and reduce these avoidable losses, manufacturers should focus on strengthening the connection between planning and execution.
Effective strategies include:
- Integrating production, warehouse, and procurement systems in real time. This ensures that material needs are automatically aligned with inventory levels, delivery schedules, and current production plans.
- Using demand forecasting tools to anticipate material requirements in advance. Automated alerts can signal when stock is approaching reorder levels, giving teams time to act before shortages occur.
- Implementing kanban-style replenishment systems to create a smooth, continuous flow of materials. These systems help eliminate manual tracking and reduce the risk of last-minute shortages by maintaining a visual or digital signal for replenishment.
Many plants already have the machinery and labor required to meet their targets. What they often lack is a reliable, disciplined approach to material flow. By improving visibility, planning accuracy, and replenishment practices, manufacturers can eliminate unnecessary delays and create a more predictable, efficient operation.
Operator Availability and Workforce Gaps
Human factors are one of the most commonly overlooked contributors to lost production time. While equipment issues often receive immediate attention, workforce-related disruptions can quietly reduce availability without being captured in formal downtime reports.
Unfilled shifts, late arrivals, and undertrained operators can lead to delays during start-up, longer changeovers, and inconsistent machine performance. These issues may not stop the line entirely, but they introduce inefficiencies that reduce total output over time.
To address these gaps, manufacturers should treat workforce planning as a critical part of uptime management. Reliable staffing and skill coverage are essential to keep production moving smoothly.
Steps to improve operator-related availability losses include:
- Tracking operator attendance and availability in relation to line performance. This helps identify patterns, such as recurring delays linked to certain shifts, teams, or times of day.
- Cross-training workers so that key equipment is not reliant on one or two individuals. A more flexible workforce can absorb absences and reduce the risk of production delays caused by staffing shortages.
- Using workforce planning tools to better align labor with production demand. This includes forecasting peak periods, balancing workloads across shifts, and ensuring that qualified personnel are assigned where they are needed most.
Even the most advanced machines cannot operate at their best without skilled and available operators. By applying the same discipline to labor planning as you do to equipment maintenance, you can reduce avoidable downtime and improve the overall stability of your operations.
Why Availability Improvements Pay Off Fast
The best part of focusing on Availability? The impact is immediate and compounding. For example, improving uptime from 80% to 88% on a critical bottleneck machine can unlock thousands of additional units per month without adding headcount or capital investment.
But the true value isn’t just in output. Higher Availability builds operational stability. It gives your team more room to plan, fewer fire drills, and more predictability across the entire plant.
When uptime becomes reliable, performance and quality improvements become dramatically easier to achieve.
Boosting Performance: Find and Fix Hidden Speed Losses
At first glance, a running machine feels like a win. But here’s the trap: not all runtimes is equal.
Machines that are technically “up” may still be running far below their ideal throughput due to performance losses, and many of these are so subtle, they escape ay-to-day visibility. Over an 8-hour shift, a few seconds shaved off each cycle or repeated micro-stops can result in hundreds of units lost without anyone noticing.
This is why improving the Performance component of OEE requires a different mindset. It’s not about whether your machines are working. It’s about whether they’re working at their full potential.
Micro-Stoppages: The Silent Killers of Throughput
Micro-stoppages are short, often unnoticed interruptions—usually lasting less than a minute—caused by small jams, misfeeds, alignment issues, or sensor glitches. Operators typically fix them on the spot without logging the event, so these stops rarely make it into performance reports.
Why they matter? Even minor pauses, when repeated dozens or hundreds of times per shift, can quietly drain 5–10% of your total production capacity - without ever triggering an alarm.
How to address them:
- Deploy IoT or edge devices that automatically detect and timestamp every micro-stop.
- Categorize stoppages by frequency and cause to identify and focus on the biggest recurring issues.
- Standardize responses and resolution protocols so operators can fix common problems faster and more consistently.
By surfacing these "invisible losses", manufacturers can make big gains with small, focused fixes.
Suboptimal Operator Settings
Even the most advanced equipment cannot deliver consistent results without precise setup. Machines depend on accurate inputs such as feed rates, temperatures, pressures, and speeds. When operators enter these values incorrectly, whether by mistake or due to inconsistent training, it can lead to slower cycle times, variation in product quality, and accelerated equipment wear.
These types of performance losses often go unrecognized because the machine is still running and producing. However, over time, small deviations in setup can create a noticeable impact on throughput and reliability.
One of the fastest and most effective ways to improve performance is by standardizing machine settings across products, shifts, and teams. Reducing variability at the setup stage creates a more stable baseline for production and reduces the chance of avoidable slowdowns.
To improve consistency and reduce setup-related losses, manufacturers should consider the following practices:
- Define and document the correct machine parameters for each product, including feed rates, cycle speeds, and process temperatures. This information should be easily accessible and regularly updated.
- Use digital work instructions or recipe lock-in systems to guide operators through setup procedures and limit the risk of deviation. These tools can ensure that every operator, regardless of shift or experience, follows the same procedures.
- Monitor and track operator input changes over time. If certain teams or individuals regularly deviate from standard settings, this can highlight training gaps or a need to revisit baseline configurations.
Standardization is one of the most powerful tools for improving performance across a production environment. It ensures that machines are operating within their designed parameters and that outcomes are repeatable from shift to shift.
By minimizing variation in how equipment is configured, manufacturers can reduce errors, protect machine health, and maintain a higher level of overall efficiency.
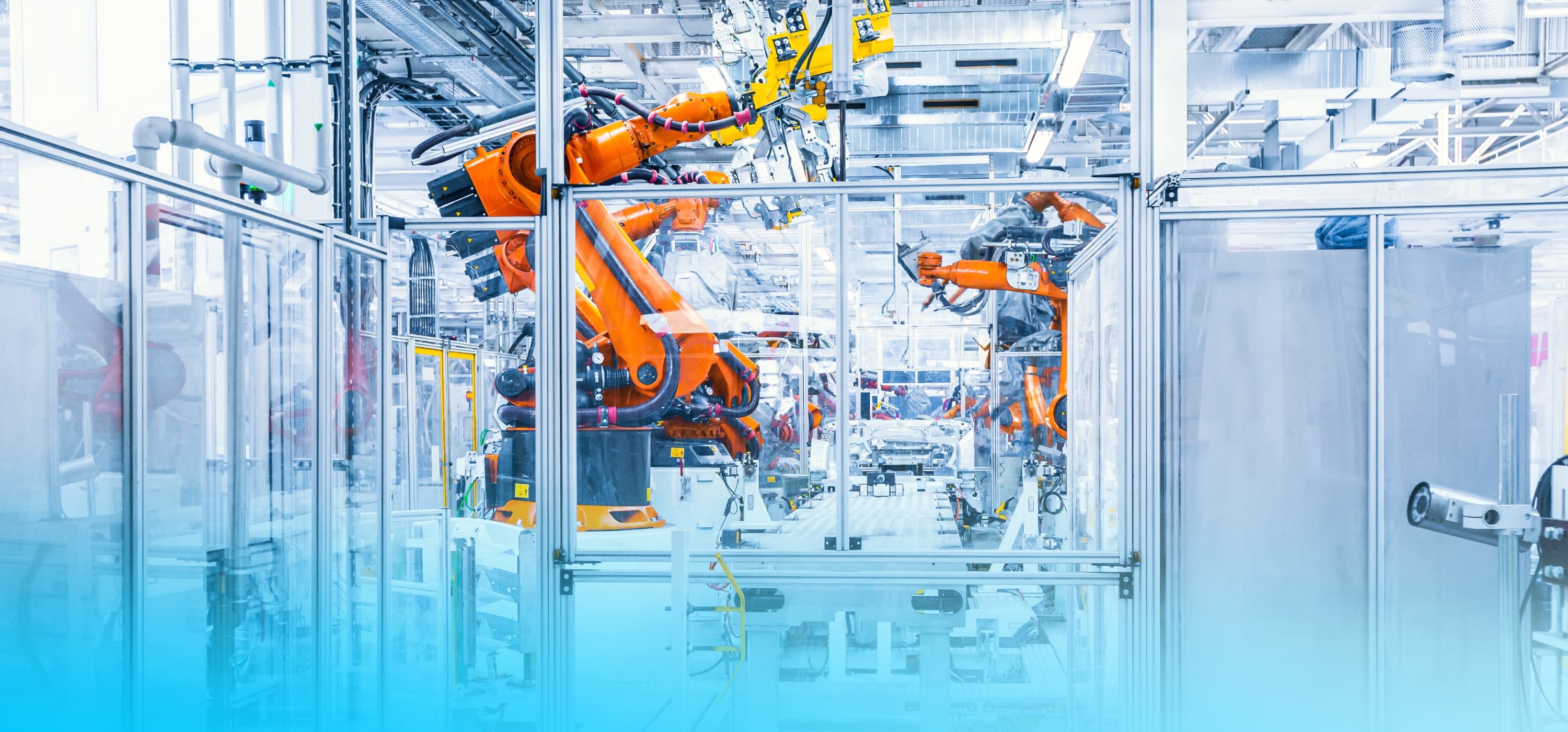
Mechanical Wear and Hidden Performance Losses
As machines age, performance can decline gradually in ways that are difficult to spot day to day. Increased friction, loose belts, worn components, and slower sensor responses can all lead to a slow but steady reduction in speed and efficiency. The equipment still operates, but it no longer performs at its original level. These small inefficiencies often go unnoticed until they accumulate into a significant drop in throughput.
Because these losses are not dramatic, they tend to be overlooked during routine maintenance or shift reviews. Yet over time, they can limit your ability to meet production targets, increase energy consumption, and reduce the predictability of your operations.
To address these hidden issues, manufacturers need to shift from reactive maintenance to a performance-focused approach. This means looking beyond just preventing breakdowns and focusing on preserving the speed and consistency of production.
Practical steps include:
- Analyzing long-term performance data across machines to identify subtle declines. This can involve comparing cycle times, reject rates, or energy usage over time to detect patterns.
- Creating digital twins of key assets to model and compare expected performance against current behavior. These virtual models help teams pinpoint where and how machines are drifting from their optimal state.
- Incorporating performance-based metrics into maintenance planning. Instead of relying solely on time-based or usage-based schedules, use indicators like cycle time variation or increased micro-stoppages as early warning signs for servicing.
Maintenance programs that focus on speed preservation, not just failure prevention, are better equipped to protect output quality and plant efficiency. By catching small degradations early, manufacturers can keep lines running at their full potential without sudden surprises or production dips.
This proactive approach not only extends equipment life but also ensures that every machine continues to contribute at the level it was designed for.
Upstream Bottlenecks and Process Sync Issues
Not all performance issues originate at the machine itself. In many cases, the real problem lies upstream - with the processes, stations, or systems that supply materials or components.
When upstream operations deliver parts inconsistently, or if conveyors batch and release materials unevenly, the result is predictable: your machine slows down or sits idle, waiting for input. These delays may be brief and irregular, but they create a ripple effect of lost time and unstable performance throughout the line.
This type of inefficiency often goes unnoticed because the machine is technically available and operational. Yet it cannot perform at full speed without a steady, well-paced supply.
How to fix it:
- Use buffer zones or WIP (Work-in-Progress) sensors to regulate material flow between stations. This helps absorb slight variations in pace and prevents downstream starvation.
- Monitor line balancing and pacing metrics to detect where one part of the process is consistently falling behind. Identifying these imbalances is critical to leveling output.
- Implement synchronization protocols so that connected machines and processes stay in sync. This can include timing adjustments, automation logic, or reconfiguring workflows for smoother transitions between steps.
Many speed losses are not caused by the machine itself, but by how the production system around it is organized. When you improve coordination and flow upstream, you reduce idling, increase consistency, and free up performance capacity that already exists within your line.
Fixing systemic flow problems is one of the most effective ways to boost throughput without changing your equipment.
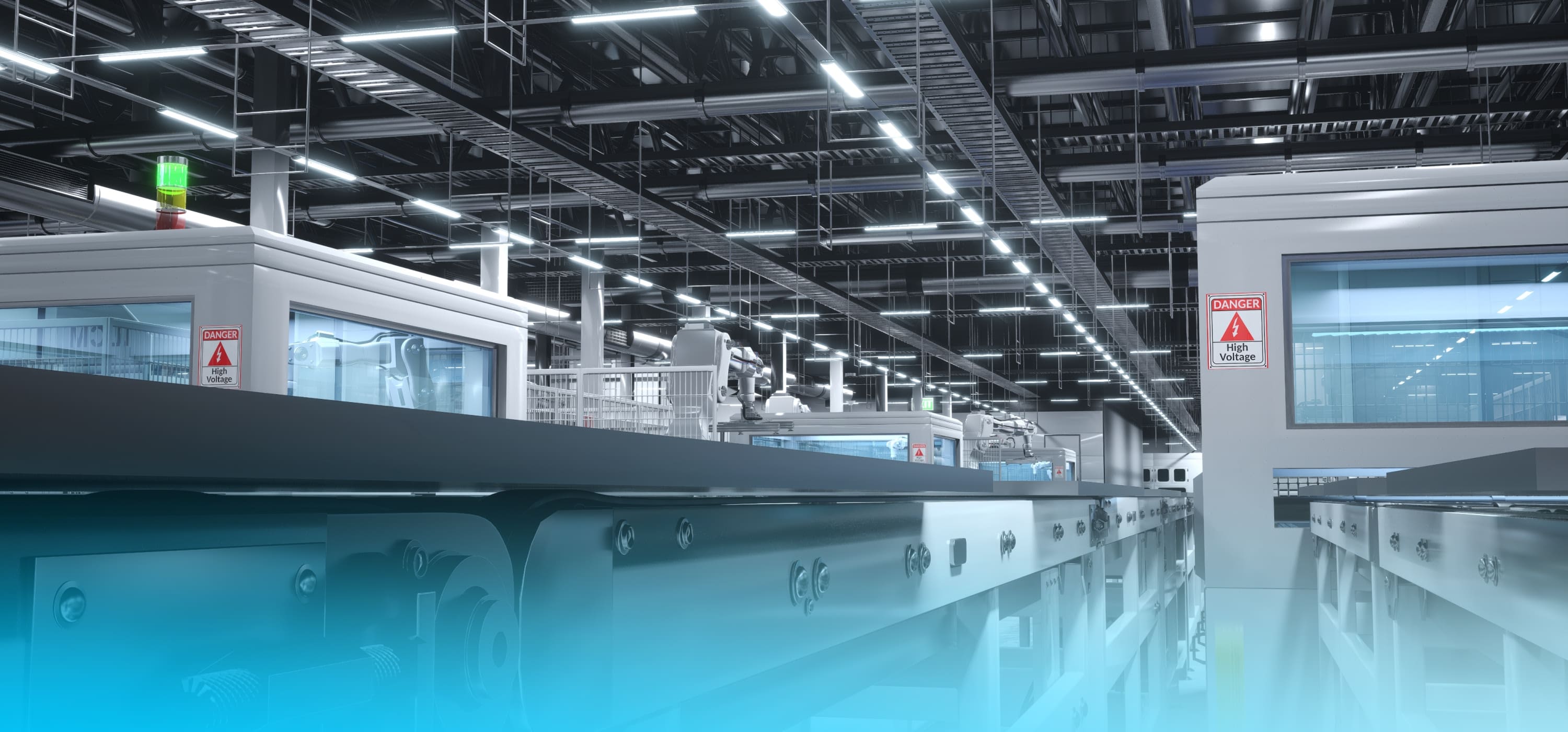
Turning Data into Real-Time Action
Having accurate data is important, but timing is what truly drives results. Operators need real-time visibility into what is happening on the line, not just a report at the end of the shift.
Dashboards that show key metrics such as cycle time deviations, micro-stop frequency, hourly targets versus actual performance help operators spot issues as they occur and make immediate adjustments. This kind of visibility allows for faster decision-making and helps prevent minor problems from becoming major disruptions.
When operators know their performance minute by minute, they can take control of the process. Instead of reacting after the fact, they can keep production on track in real time.
The Big Miss: Underestimating Cumulative Loss
One of the most common mistakes in performance improvement is focusing only on major breakdowns or large, visible gaps. While those issues are important, they often overshadow the smaller, more consistent losses that occur across products, shifts, and lines.
These micro-losses tend to slip through the cracks. They often go unnoticed because:
- They do not trigger alarms
- They are not consistently logged or flagged by operators
- They rarely receive structured root cause analysis
Yet over time, these seemingly minor inefficiencies can add up to significant throughput loss. Because they are repeated day after day, they represent some of the most fixable and impactful opportunities for improvement in the entire plant.
Capturing and addressing micro-losses requires a shift in mindset. It means paying attention to the small delays, the slight deviations, and the recurring slowdowns that are easy to ignore. When manufacturers develop the systems and habits to detect and respond to these patterns, they often unlock capacity without needing to invest in new equipment or labor.
Performance Wins Compound Quickly
When it comes to improving OEE, performance is often the most overlooked opportunity, but also one of the most accessible.
Small changes can lead to significant results. For example, reducing cycle time by just 0.5 seconds per unit can recover hours of production time each week. If a line produces 10,000 units a day, that half-second gain adds up to more than an hour of regained capacity per shift. When applied across multiple lines or facilities, the impact becomes even more substantial.
These are the kinds of improvements that scale. They do not require large capital investments or major process overhauls. Instead, performance improvements typically rely on operational discipline and smarter use of existing systems.
Unlike quality or downtime fixes, which may involve new equipment, retraining, or process redesign, performance improvements can often be achieved by focusing on three areas:
- Better visibility: Providing operators and supervisors with access to real-time data, cycle time trends, and alerts for early intervention.
- Tighter discipline: Standardizing work practices, enforcing target cycle times, and addressing small delays consistently.
- Systems that connect insights to action: Integrating machine data with workflows so that the right people can respond quickly when performance drops.
With this approach, performance improvement becomes part of the daily rhythm. It shifts from being a project to becoming a habit. Over time, these small, continuous gains drive meaningful and measurable increases in overall efficiency.
Raising Quality: Address Defects Before They Escalate
In high-volume manufacturing, even a small defect rate can have a major impact. A one or two percent scrap or rework rate may seem acceptable at first glance, but over time, those losses quietly chip away at your margins. Defective products do more than waste raw materials. They also consume valuable machine time, labor hours, packaging, and logistics capacity. In many cases, the cost of rework exceeds the cost of prevention.
Beyond the operational costs, recurring quality issues erode customer confidence. A defect that reaches the end user can lead to service calls, returns, warranty claims, or even damage to your reputation. The further a defect travels through your process before it is caught, the more expensive it becomes to correct.
The bigger concern is that most defects are not random or isolated. They are often indicators of deeper, systemic weaknesses. These may come from a misaligned tool, a poorly calibrated setting, inconsistent materials, or a lack of operator training. The defect is the result, not the root cause.
Leading manufacturers recognize this and take a proactive approach. Rather than simply responding to quality problems as they appear, they focus on building systems that can detect and correct problems early. These systems are designed not only to reduce defects, but also to create a continuous feedback loop for improvement.
When quality data is captured in real time and tied back to specific inputs, people, and processes, it becomes possible to identify trends and make targeted improvements. A small adjustment upstream can prevent a recurring issue downstream. Over time, this leads to more stable operations, higher first-pass yield, and greater customer satisfaction.
Improving quality is not just about catching bad parts. It is about building a process that consistently produces good ones.
Common Sources of Quality Losses
Defects in manufacturing rarely happen all at once. In most cases, they develop gradually as small variations go unnoticed. A single rework or scrap part may not raise concern, but when those issues repeat across shifts and batches, they start to take a serious toll on productivity and OEE.
To improve quality, it is important to first understand where defects typically come from:
- Tool wear or poor calibration. Over time, tools and equipment naturally wear down. Even small misalignments can lead to dimensional drift, inconsistent surface finishes, or off-spec parts that require rework or are scrapped entirely.
- Inconsistent raw materials. Variability in the inputs, such as differences in hardness, viscosity, moisture content, or color, can disrupt a process that otherwise runs smoothly. Even within the same supplier batch, slight variations can impact product quality.
- Outdated work instructions. When operators rely on printed documents or legacy procedures that are not up to date, small inconsistencies creep into the process. These can lead to deviations that are hard to catch until defects begin to show up in higher numbers.
- Operator error or insufficient training. In environments with multiple shifts or frequent staff rotations, quality can suffer if training is inconsistent or if operators are unfamiliar with complex assemblies. What begins as a minor deviation may repeat across many units before being detected.
These sources of quality loss are not always immediately visible. A few reworked parts or a small amount of scrap may seem tolerable in isolation, but over time they compound into a much larger problem. Without a structured approach to identifying and addressing the root causes of defects, these issues can become the primary factor holding back improvements in overall equipment effectiveness.
By understanding and monitoring the early signs of quality drift, manufacturers can prevent small issues from escalating and protect both output and customer satisfaction.
Embed In-Line Inspection and Early Detection
The sooner a defect is identified, the easier and less expensive it is to correct. Waiting until the end of a production run to discover issues leads to rework, scrap, and missed delivery deadlines. In contrast, in-line inspection allows manufacturers to catch problems immediately, while there is still time to adjust the process.
In-line inspection systems can range from simple sensors to advanced machine vision technologies. These tools are capable of detecting a wide variety of issues, including:
- Missing components
- Deviations in shape, color, or size
- Surface damage or contamination
- Incorrect assembly or alignment
By embedding these checks directly into the production line, manufacturers can take action in real time. This approach allows teams to:
- Eliminate defective parts before they accumulate or move downstream
- Prevent damage to equipment or final products that may occur from processing faulty inputs
- Give immediate feedback to operators, enabling faster response and reducing the risk of recurring errors
In-line inspection should be viewed as an active quality control system, not a retrospective audit. It shifts quality assurance from being reactive to being part of the real-time workflow. This not only improves output but also empowers the production team to maintain high standards with confidence and consistency.
Use Statistical Process Control (SPC) to Predict Drift
Most defects are not caused by sudden, isolated events. In many cases, a defective part is the final symptom of a slow, gradual deviation in the process. This kind of variation often goes unnoticed until it creates a visible problem. By then, several defective parts may already have been produced.
Statistical Process Control, or SPC, is a method used to monitor key process variables over time. It helps detect early signs of instability before they result in off-spec products. By collecting and charting data points such as temperature, torque, pressure, or speed, manufacturers can maintain tighter control over process behavior.
When implemented effectively, SPC allows teams to:
- Detect process drift early, before it causes defects
- Identify patterns that suggest equipment wear or inconsistent raw materials
- Evaluate whether changes to process inputs are improving or hurting stability
SPC is not limited to organizations following Six Sigma or advanced lean programs. It is a foundational practice for any manufacturer that wants to reduce variability and maintain consistent output. The insights it provides help teams move from reactive problem-solving to proactive process control.
By integrating SPC into daily operations, manufacturers gain a clearer picture of where variability is entering the system and how to correct it before it impacts quality or throughput.
Upgrade Training and Standard Operating Procedures (SOPs)
Even in highly automated environments, people remain central to delivering consistent product quality. In fact, the more complex or manual the task, the greater the risk of variation between operators. While automation can reduce certain types of errors, human involvement still plays a key role in setup, inspection, and judgment-based tasks.
Improving training is not just about doing more of it. It is about making training smarter, more accessible, and more relevant to each role.
To reduce variability and improve execution on the shop floor, manufacturers should consider the following best practices:
- Replace printed SOPs with digital work instructions that include version control and embedded content such as videos, images, or interactive guides. These tools provide clearer, more engaging guidance and are easier to update.
- Tailor training content to reflect each operator’s role, experience level, and the complexity of the product or task. A one-size-fits-all approach is less effective than targeted, role-specific learning.
- Use training data to identify knowledge gaps across shifts or teams. By tracking training completion, performance metrics, and error rates, managers can better understand where additional support or coaching is needed.
When operators have real-time access to clear, contextual instructions, they are better equipped to perform tasks accurately and consistently. This reduces the chance of errors, improves first-pass yield, and builds quality into the process from the start rather than relying on inspections at the end.
Smart training strategies create a more capable workforce, reduce performance variability, and make it easier to maintain high standards across multiple shifts and product lines.
Build a Learning Loop for Continuous Quality Improvement
Improving quality is not about reacting to every defect as it happens. It is about creating a structured system that learns from problems, adapts over time, and prevents the same issues from recurring. This requires more than detection. It requires a closed feedback loop that connects the point of failure with analysis, decision-making, and permanent improvement.
A strong continuous quality improvement system includes the following components:
- Automated logging and categorization of defects. When every defect is recorded and classified in real time, patterns emerge that may not be visible during manual reviews.
- Regular root cause analysis sessions, using methods such as the 5 Whys or cause-and-effect diagrams. These exercises help teams move beyond symptoms to uncover the true reasons why a defect occurred.
- A defined process for converting insights into action. Whether it is updating work instructions, changing materials, retraining operators, or adjusting machine settings, improvements need to be implemented and tracked over time.
The goal is to create a cycle where every defect becomes a source of learning. When that learning is turned into a process update or behavior change, quality improves not just in the short term, but over the long run.
This type of learning loop helps teams become more proactive and confident in their ability to solve problems. It also contributes directly to higher OEE by reducing rework, scrap, and disruptions caused by recurring issues.
True quality improvement comes from building a system that gets smarter with every shift, every product run, and every lesson learned.
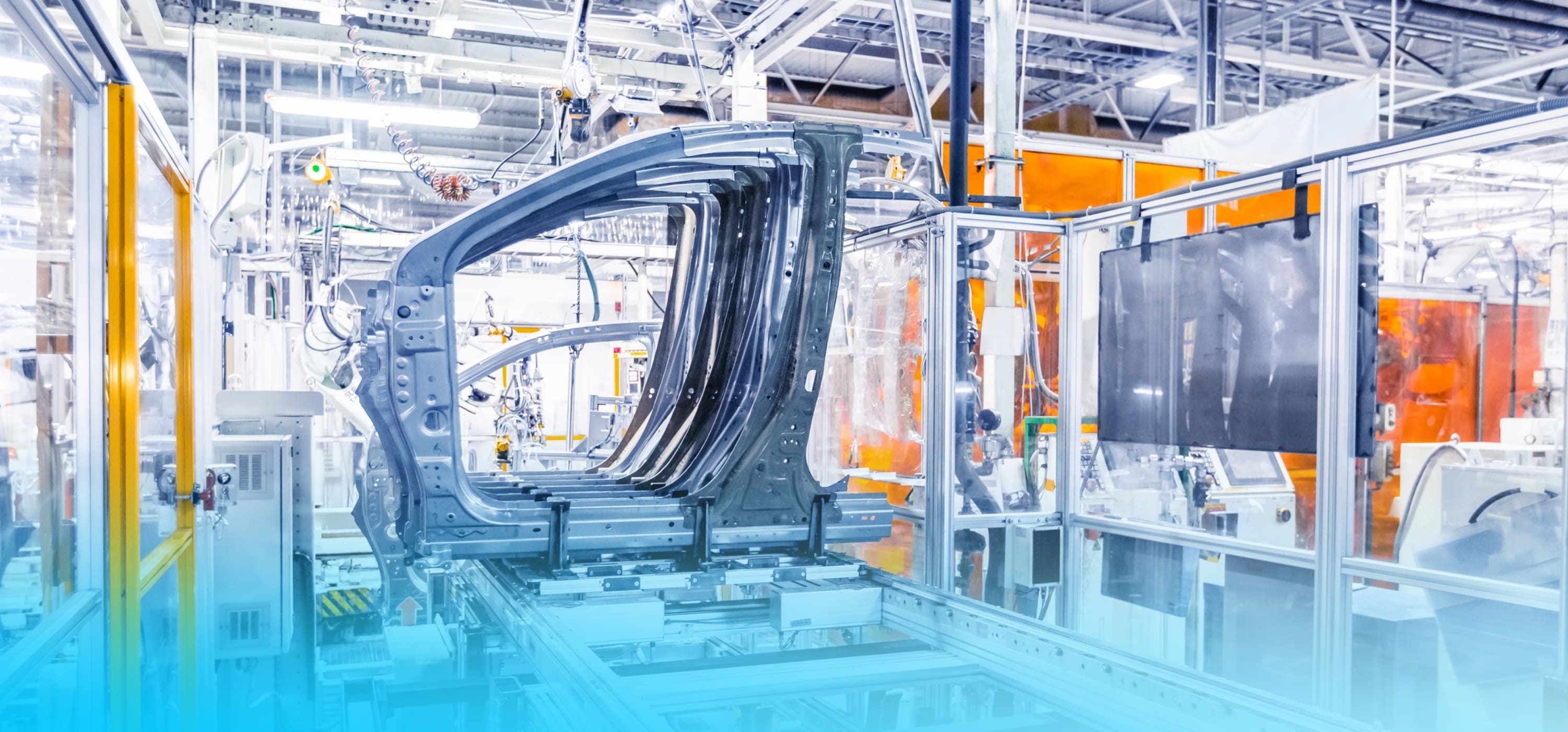
Quality Is the Foundation of Repeatability
In the end, quality isn’t just a metric - it’s a discipline. It’s about creating processes that produce consistent results, day after day, shift after shift, regardless of who’s on the line or what product is running.
If your lines are plagued by frequent rework, scrap, or customer complaints, improving quality can offer the fastest path to measurable OEE gains. And the tools to do it - inspection systems, SPC, training, analytics - are more accessible than ever.
Build a Learning Loop for Continuous Quality Improvement
Improving quality is not about reacting to every defect as it happens. It is about creating a structured system that learns from problems, adapts over time, and prevents the same issues from recurring. This requires more than detection. It requires a closed feedback loop that connects the point of failure with analysis, decision-making, and permanent improvement.
A strong continuous quality improvement system includes the following components:
- Automated logging and categorization of defects. When every defect is recorded and classified in real time, patterns emerge that may not be visible during manual reviews.
- Regular root cause analysis sessions, using methods such as the 5 Whys or cause-and-effect diagrams. These exercises help teams move beyond symptoms to uncover the true reasons why a defect occurred.
- A defined process for converting insights into action. Whether it is updating work instructions, changing materials, retraining operators, or adjusting machine settings, improvements need to be implemented and tracked over time.
The goal is to create a cycle where every defect becomes a source of learning. When that learning is turned into a process update or behavior change, quality improves not just in the short term, but over the long run.
This type of learning loop helps teams become more proactive and confident in their ability to solve problems. It also contributes directly to higher OEE by reducing rework, scrap, and disruptions caused by recurring issues.
True quality improvement comes from building a system that gets smarter with every shift, every product run, and every lesson learned.
Creating a Culture of Continuous OEE Improvement
One of the most common misconceptions about Overall Equipment Effectiveness is that it is simply a number to report. - something reviewed once a week or at the end of the month and then set aside. In reality, leading manufacturers treat ит very differently. They understand that it is not a static metric but a reflection of how well their entire operation is functioning.
OEE is not something you fix once and forget. It is a performance discipline that requires ongoing attention. Think of it as the operational equivalent of a heartbeat. It measures the health of your equipment, the consistency of your processes, and the level of engagement from your teams. Like any vital sign, it must be monitored, understood, and acted upon regularly.
The manufacturers who consistently improve OEE do not rely on one-off projects or periodic interventions. Instead, they build a culture where OEE is part of daily operations, embedded in how decisions are made, and shared across departments.
Here are key steps to build that kind of culture:
- Hold regular reviews of OEE performance that involve cross-functional teams. When production, maintenance, quality, and engineering come together to review results and plan improvements, performance gains are more sustainable.
- Set clear, targeted KPIs at the shift, machine, and product level. Breaking down goals into smaller, actionable targets makes it easier for frontline teams to take ownership.
- Recognize and reward improvement efforts from all levels of the organization. When employees see that their contributions lead to measurable results, they become more engaged and proactive.
- Create feedback loops that connect the shop floor to leadership and support teams. Make it easy for operators to report issues and for improvement teams to implement solutions.
Building a culture of continuous OEE improvement is not about adding more complexity. It is about making performance part of your daily rhythm, empowering teams with data, and giving them the tools to respond quickly and effectively.
When OEE becomes part of your organizational mindset, improvement is no longer reactive or occasional. It becomes consistent, scalable, and deeply ingrained in how you run your business.
Make OEE a Team Sport
In many manufacturing environments, OEE data is collected and reported, but rarely acted upon in real time. It often stays in the hands of a plant manager or is buried in a monthly report, reviewed too late to drive meaningful change on the shop floor.
High-performing manufacturers take a different approach. They treat OEE as a shared responsibility and make performance improvement a team effort across departments.
Instead of siloing the data, they bring it into daily operations and make it accessible to everyone involved in production. This includes operators, supervisors, maintenance teams, quality engineers, and line leaders.
Ways to build team ownership of OEE include:
- Holding regular performance reviews where operations, maintenance, quality, and engineering teams come together to review OEE metrics and identify improvement opportunities.
- Displaying real-time OEE dashboards on the shop floor, broken down by shift, line, or asset. This makes performance visible and relevant to frontline teams, not just management.
- Using data to support problem-solving, not to assign blame. When teams work with shared data and a common goal, they are more likely to collaborate openly and focus on solutions rather than pointing fingers.
When OEE ownership is shared across functions, the benefits go beyond better metrics. The speed of response improves, lessons are shared more easily, and small issues are addressed before they escalate. This collaborative approach builds a continuous improvement mindset and helps create a culture where performance is everyone's priority.
Set KPIs That Actually Drive Behavior
Plant-wide OEE goals can be useful for spotting trends over time, but they are often too broad to influence day-to-day decisions. To drive meaningful behavior change on the shop floor, performance metrics need to be more specific, localized, and actionable.
Rather than focusing only on the overall score, set granular KPIs such as:
- OEE by product line or machine center
- Availability or cycle time by shift
- First-pass yield or scrap rate by individual SKU
These metrics can be broken down further by operator group, team, or time block to create a clear sense of ownership. The more tangible and specific the goal, the more likely it is to motivate action and support targeted problem-solving.
Recognize and Reward Continuous Improvement
Most frontline teams want to do better. What they often need is visibility into their performance and recognition for the progress they make.
Consider building a recognition program that highlights:
- The team with the fastest cycle time improvements
- The shift that achieved the highest equipment availability
- The production run with the fewest defects
- Employee suggestions that led to measurable improvements in OEE
Recognition does not always require formal awards or financial incentives. A simple shout-out in a morning meeting, a spot on a performance board, or acknowledgment from a supervisor can go a long way in reinforcing positive behaviors and maintaining momentum.
Digitize the Feedback Loop
The most effective continuous improvement systems share one critical feature: a fast, reliable feedback loop between the shop floor and the teams responsible for support and decision-making.
When operators encounter an issue, they should be able to:
- Log the event quickly, using a digital tool or voice command
- Tag the issue for root cause analysis
- Notify the appropriate team, whether that is maintenance, engineering, or quality
At the same time, engineers and supervisors need access to tools that allow them to:
- Analyze that data in near real time
- Deploy corrective actions efficiently
- Close the loop by reporting back to the team that flagged the issue
When this loop is digitized it becomes easier to turn insight into action and action into long-term learning.
Empowerment Is the Missing Link
OEE programs often fail not because the data is wrong, but because the people who can act on it are not engaged or equipped to do so. Ownership is unclear, and improvements stall as a result.
When frontline teams are empowered to take ownership of performance metrics, suggest improvements, and see the impact of their decisions, the organization becomes more agile, more accountable, and more resilient. Improvement no longer depends on management intervention alone. It becomes part of the culture.
The manufacturers who lead in OEE do more than measure it. They build systems and mindsets that support daily improvement at every level.
Use Data, Not Just Discipline
Improving OEE is not only about discipline on the shop floor. It is also about having the right systems in place to make fast, informed decisions. The companies that succeed are those that move beyond spreadsheets and disconnected reports toward a connected, data-driven operation.
This is where Customertimes can help. We specialize in helping manufacturers modernize and optimize their operations. From integrating MES and IoT data to deploying AI-driven recommendations, we work with your team to reduce downtime, improve performance, and ensure quality is built into every step.
Our solutions are never one-size-fits-all. We tailor our approach to match your production environment, your level of digital maturity, and your business goals. If you are ready to make OEE improvement part of your daily operations, start with the systems and insights that make it possible.
Contact us to schedule a manufacturing performance assessment, and let’s explore how we can help you drive smarter, faster, and more sustainable improvements.